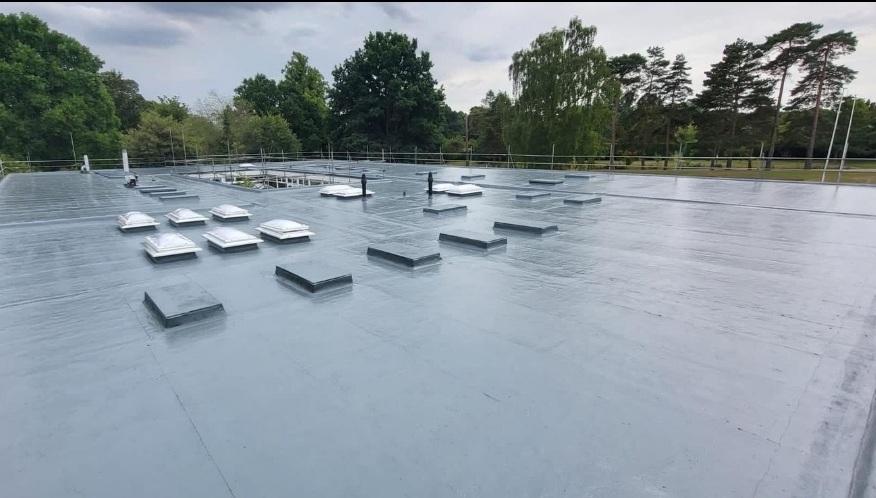
Liquid Applied Roofing: Why Is It So Popular Now?
With an increased focus on safer working practices in the construction industry, the products used on buildings are under closer scrutiny than ever before. Many sites are now insisting on flame-free working areas. This has had a direct impact on certain roofing systems. This includes torch-on felts and hot melt systems.
Hot work on flat roofs is an extremely high-risk process. It poses a big fire risk to contractors as well as to the building and its occupants. Injuries are common and an accident can shut a site down for days. This can cause added cost to any construction project. Also, the increasing lack of qualified hot works applicators and a reduction in their skill levels has added to the risk of installing hot systems.
This has led to many roofing companies to reconsider their product range or at least add liquid systems as an alternative.
The Growth Of Liquid Roofing Systems
Cold applied liquid roofing is the fastest-growing roofing system specified for construction projects. These systems are flame free, although some contain varying levels of harmful solvents and other chemicals and care must be taken. However, they are still considered a safer option than those requiring naked flame. Especially low odour liquid waterproofing systems.
An industry report stated, in the last twelve months alone the global liquid waterproofing market is expected to grow from £5.1 billion to upwards of £6.1 billion, reaching over £8 billion in 2026, which is a remarkable increase. It is, therefore, reasonable to expect the growth of the liquid waterproofing market in the UK to follow a similar upward trajectory as the rest of the world. Liquid waterproofing has been the fastest-growing sector of the flat roofing market, growing at a rate of nearly 70% in the past 5 years.
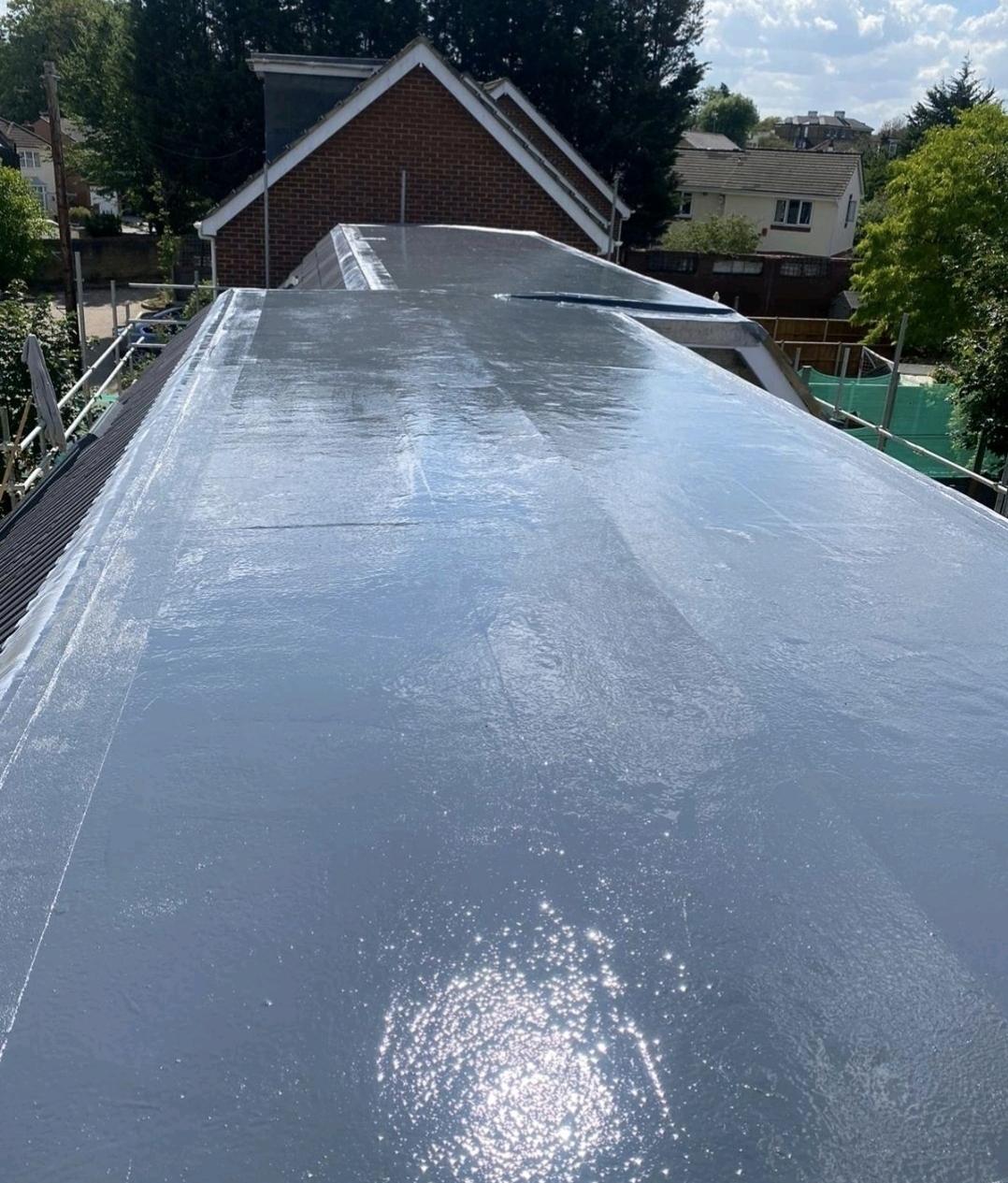
This equates to 30% of the roofing industry, demonstrating the increased importance of these systems. Liquid coatings are used in construction today, including silicones, acrylics, and polyurethanes. These weren’t introduced until the 1960s and 70s. Liquid roofing is considered very energy efficient. With the growing requirement of energy efficient homes in the UK, this is expected to fuel the growth of liquid waterproofing systems, which is already accelerating due to it being considered a safer waterproofing system.
For instance, 85% of new homes built in the UK last year were band A or B energy efficient. Hence, the obvious increase in liquid roofing solutions. Also, during this period of economic uncertainty, there will be a decline in new roof construction and renovation. Because of this, many roofing companies will need to downsize their workforces and seek out more cost-effective methods to provide value to their customers. A notable area in which savings have been made using liquid applied roofing is for refurbishment projects. One example, is in cut edge corrosion treatment. Using a liquid applied coating on cut edge corrosion can considerably extend the lifespan of an industrial roof. The coating will not only remedy any cut edge corrosion but will immediately make the existing roof waterproof. As more traditional roofing companies began adapting liquid roofing practices, they also began training their employees in the technology.
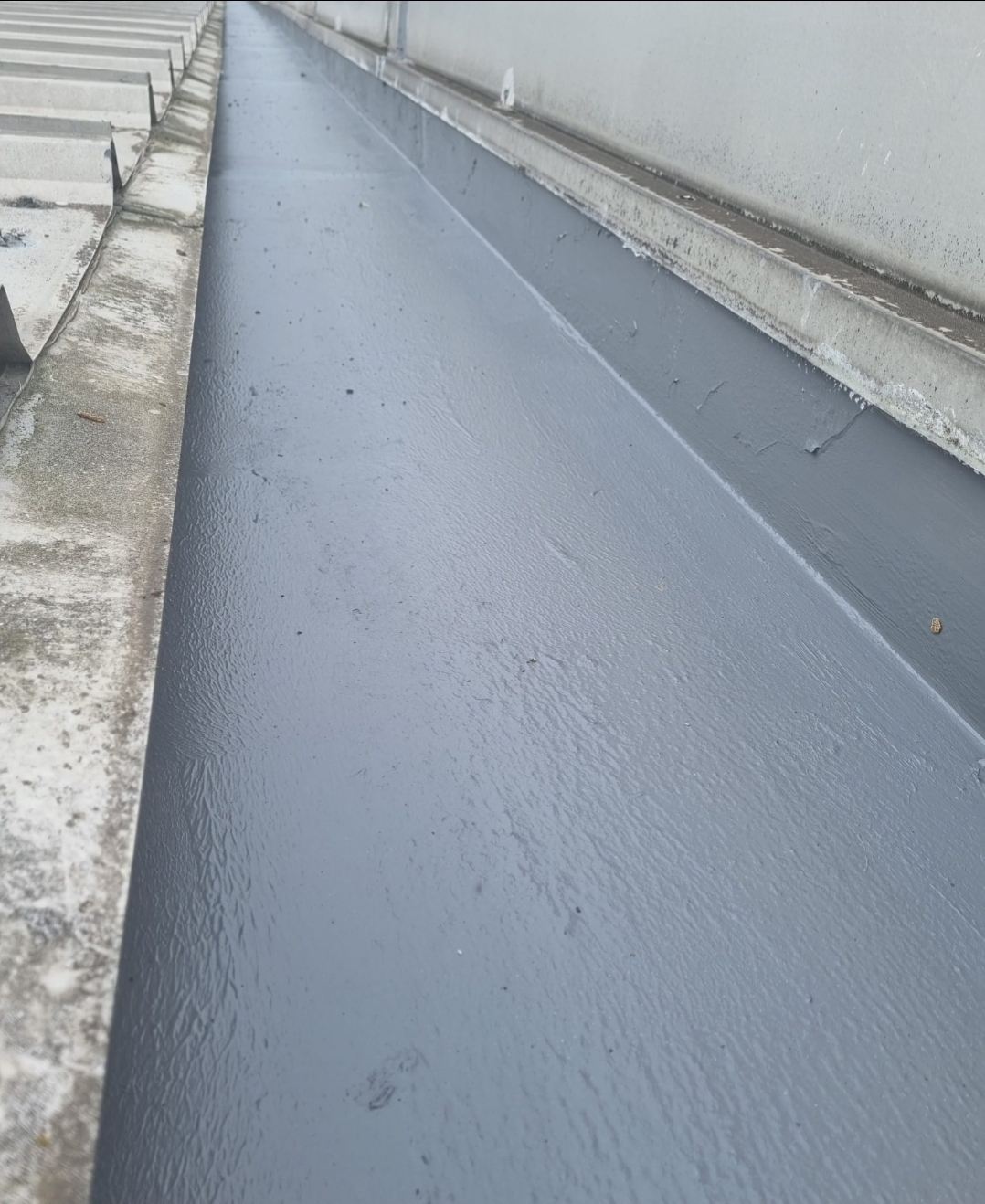
Flat Roof Installations Using Liquid Systems Require Less-Skilled Labour
The installation of a liquid waterproofing system requires less-skilled labour than traditional roof refurbishments and replacements. This obviously saves contractors on the cost of training and labour. This will incentivise many commercial roofing companies to switch to liquid applied waterproofing systems out of necessity. Many roofing companies will have reduced workforces, and this also goes hand in glove with liquid roofing which requires less labour.
Liquid waterproofing can be undertaken with high quality materials. Many of the products used have been independently tested and their performance verified. In the United Kingdom, the leading testing and approvals company is the British Board of Agrément (BBA) which has been issuing approvals for liquid roofing systems since 1975. This means any BBA certified product should offer excellent performance when used for liquid applied waterproofing systems.
How Liquid Systems Waterproof Flat Roofs
A basic understanding and overview enable us to understand the increase in popularity of cold applied liquid systems. A liquid coating is applied to the surface of the flat roof. This system is rapid curing to create a seamless, UV-resistant, and waterproof membrane. Liquid roofs act as a barrier protecting roof substrates from both the sun and rain.
The coating cures to form an elastomeric waterproof membrane. This means that they are very capable in dealing with building movement. Often, but not always, they are fully reinforced with a glass fibre or polyester matting. Liquids can stretch and return to its original shape without damage. The coatings can be applied over most traditional roofing materials, including felt, asphalt, bitumen, and concrete. Again, unlike the installation processes of felt, asphalt and bitumen membranes, liquid applications are flame free.
The liquid coating material used is applied cold, thus cutting out fire risk. It can be used for many solutions including:
- Roof covering (new or existing roof systems)
- Balconies
- Walkways and floors
- Gutter lining
- Hard-to-detail areas
- Cut edge corrosion
- Asbestos encapsulation
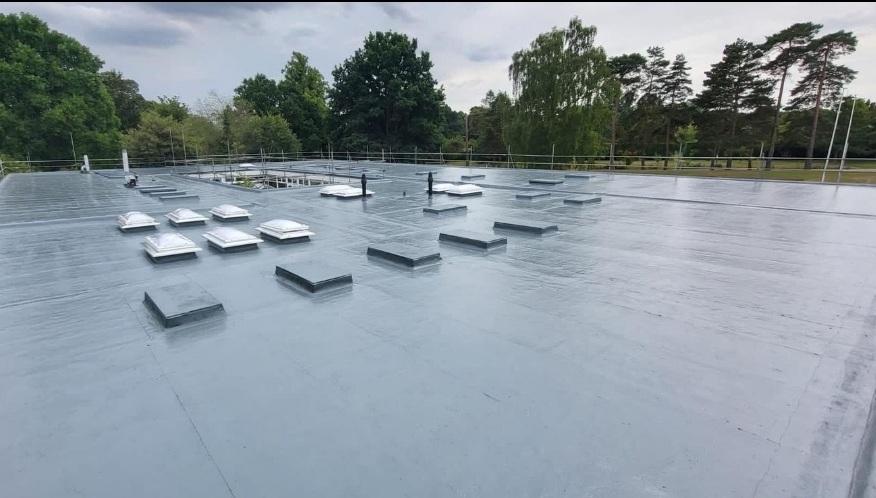
There is a growing understanding of the need to eliminate seams and laps on roofs as these are weak points. Completely seamless waterproofing systems are proven to have fewer failures. Bolder designs are also possible using curves and angles. These materials have improved considerably over the past few decades and form the basis for most modern liquid membrane roofing systems.
Liquid Applied Roofing Can Be Used On Several Roof Designs
Liquid roofing is the application of a specialist liquid roof coating. It can be applied to most roof designs, such as flat, pitched, and curved ones. When installed, liquid roofing systems encapsulate the surface, in effect preserving the substrate underneath and protecting it from weathering.
This is especially effective when dealing with asbestos roofs, as attempted removal of asbestos roofing can be very dangerous, releasing material that can trigger asbestosis. Using a liquid coating system encapsulates the asbestos, therefore making disturbance of the material unlikely.
PU liquid is considered one of the best waterproofing materials. It can be applied seamlessly and penetrates the surface deeply and evenly. Liquid waterproofing can fill in even the fine cracks in concrete, reducing its water absorption. It is the ideal solution for complex detailing. It can provide high performance waterproofing to hard-to-reach areas such as pipes, HVAC, various awkward details and anything else on the roof that makes it difficult to waterproof. Importantly, liquid roofing does not cause noise disturbance during installation, and they are often very low odour.
Liquid waterproofing membranes should have a minimum life expectancy of 10 years. However, they can last up to 25 years with the correct maintenance and system. Roof coating systems do not require a complete roof tear-off. They are applied directly on top of the existing roof deck, eliminating everything involved in a roof removal, this dramatically cuts costs.
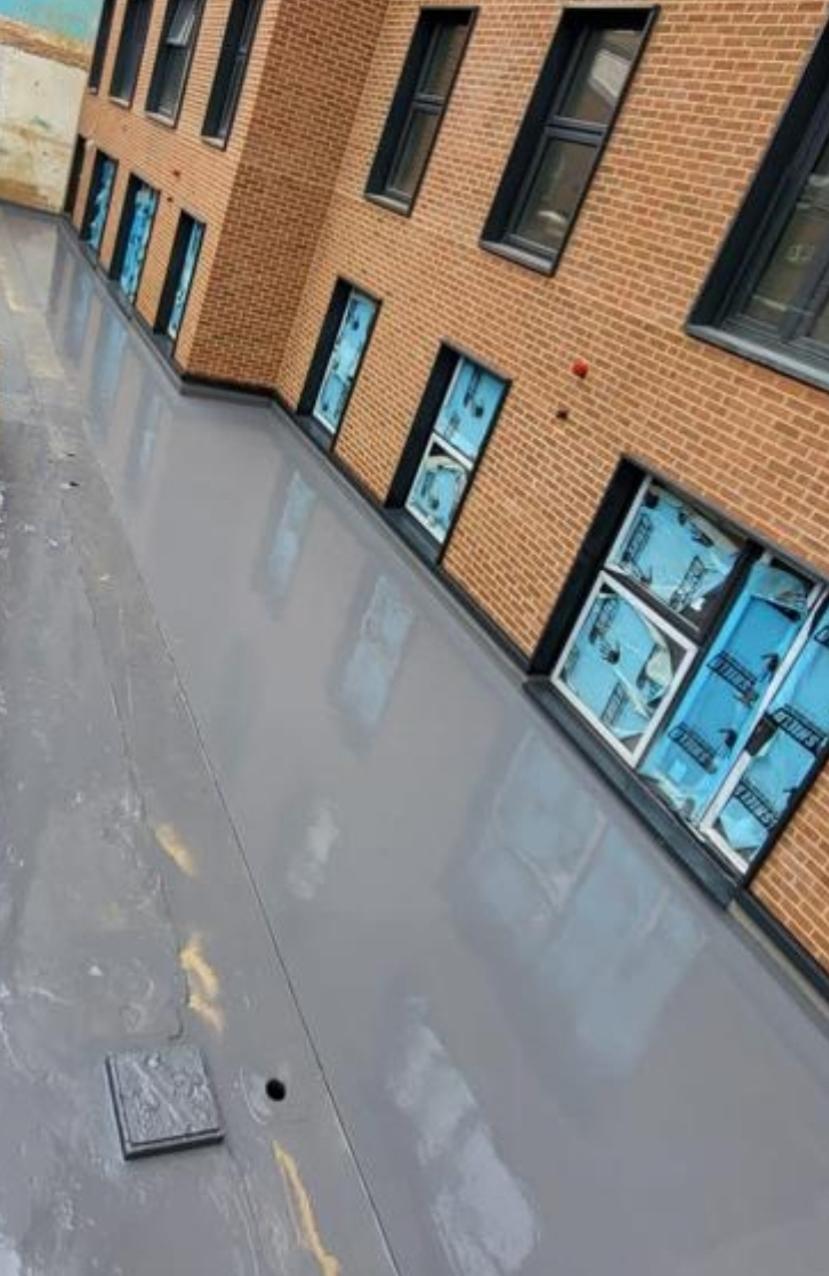
Cold Applied Liquid Waterproofing Saves Time
Using a liquid roof coating system removes the extensive labour and time of cutting and sizing sheets of roofing material to work around all the details you find on top of the roof, plus the saving in time due to the shortened construction phase. This is particularly appealing on projects which involve large commercial roofs. A liquid roof coating system offers excellent waterproofing due to its seamless and monolithic membrane.
As mentioned previously, all roofs need to expand and contract, most roofs have seams and/or nails which take the brunt of the tension caused by the expansion and contraction (this is considerable in the UK where there is a probability of extreme temperatures in both summer and winter. Over time, it is common to find roof leaks and failures at these seams. They are the weak point on any roof.
Low-sloped roofs are often referred to as flat roofs; however, the pitch on a low-sloped roof is greater than that of a flat roof, which is 0-2 inches. Low-sloped roofs are designed with pitch, to allow water to flow off the rooftop into a proper drainage system.
A dry roof is always the most efficient as ponding of water can increase the likelihood of a leak, and can promote algae or mould to form, causing damage to the roofs surface. This allows your roof to move with the building as it expands and contracts during different temperature changes throughout the day.
In summary, liquid roofing has proven to be a cost-effective option. Its costings are one of the main things that make it a viable as a roofing solution. Liquid roofing benefits include:
- Little maintenance
- Fast curing and waterproof immediately upon application
- Safer and easier to install
- Avoidance of any fire risk as it can be applied without any hot works
- Provide very little disruption when being installed
- Excellent for extending roof life and lowering roof maintenance
- Allows restoration of existing roofs, saving costly roof replacement costs
- Can last up to 25 years
- Applying over an existing roof area eases the strain on congested landfill sites
- Cost-effective solution saving on project costs for installers and clients alike
- Suitable to use for green roof systems
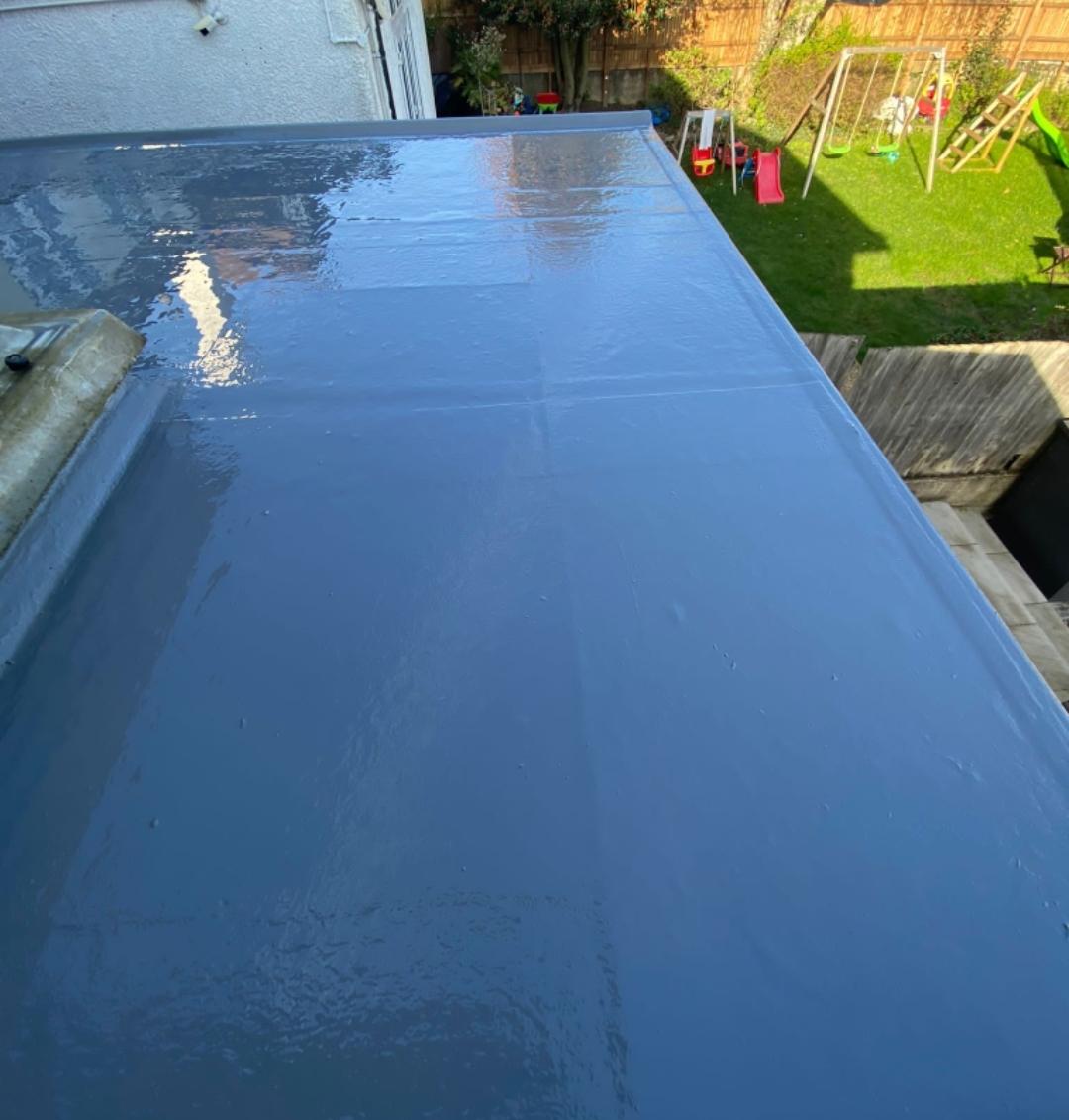
The use of liquid membranes is proving to be the future regarding roof design for all the reasons mentioned above. The roofing industry looks all set to embrace this ever-improving technology and housing design will reflect this over the coming years. That is why, we at Chandlers, have been increasing the range of liquid waterproofing products and we will be happy to answer any questions you have about these solutions.